Engineering services company HCS used their newly purchased RealWear headset and Librestream’s Onsight software to initiate a hands-free, assisted reality support call to help correctly install an innovative FitMachine IIoT sensor from MOVUS Australia.
HCS looks to technology to provide more connected services
As a major global hub of natural gas production, Western Australia hosts a large number of leading oil and gas operators, as well as numerous world-class engineering businesses that provide the services and equipment needed to discover, extract, process, and transport valuable energy resources.
These service companies are required to operate with extremely compliant and efficient processes and systems in a tightly regulated and highly competitive industry. They typically operate in remote locations and compete for a limited pool of highly specialised workers.
These conditions drive technology-led innovation.
HCS engineers provide their customers with highly specialised support of critical production equipment, located in some of the most remote areas of Western Australia. To deliver this work, HCS provides its customers direct access to a wide range of engineering specialists around the world.
HCS is an international engineering services company renowned in the oil and gas sector for the design and manufacture of Intervention Workover Control Systems (IWOCS), production control systems and subsea assemblies.
Emerging Australian sensor technology to enable smart services
Behemoth Technology recently supported HCS to trial industrial monitoring technology from Queensland-based company MOVUS Australia, allowing them to further harness technology to better service their remote customers.
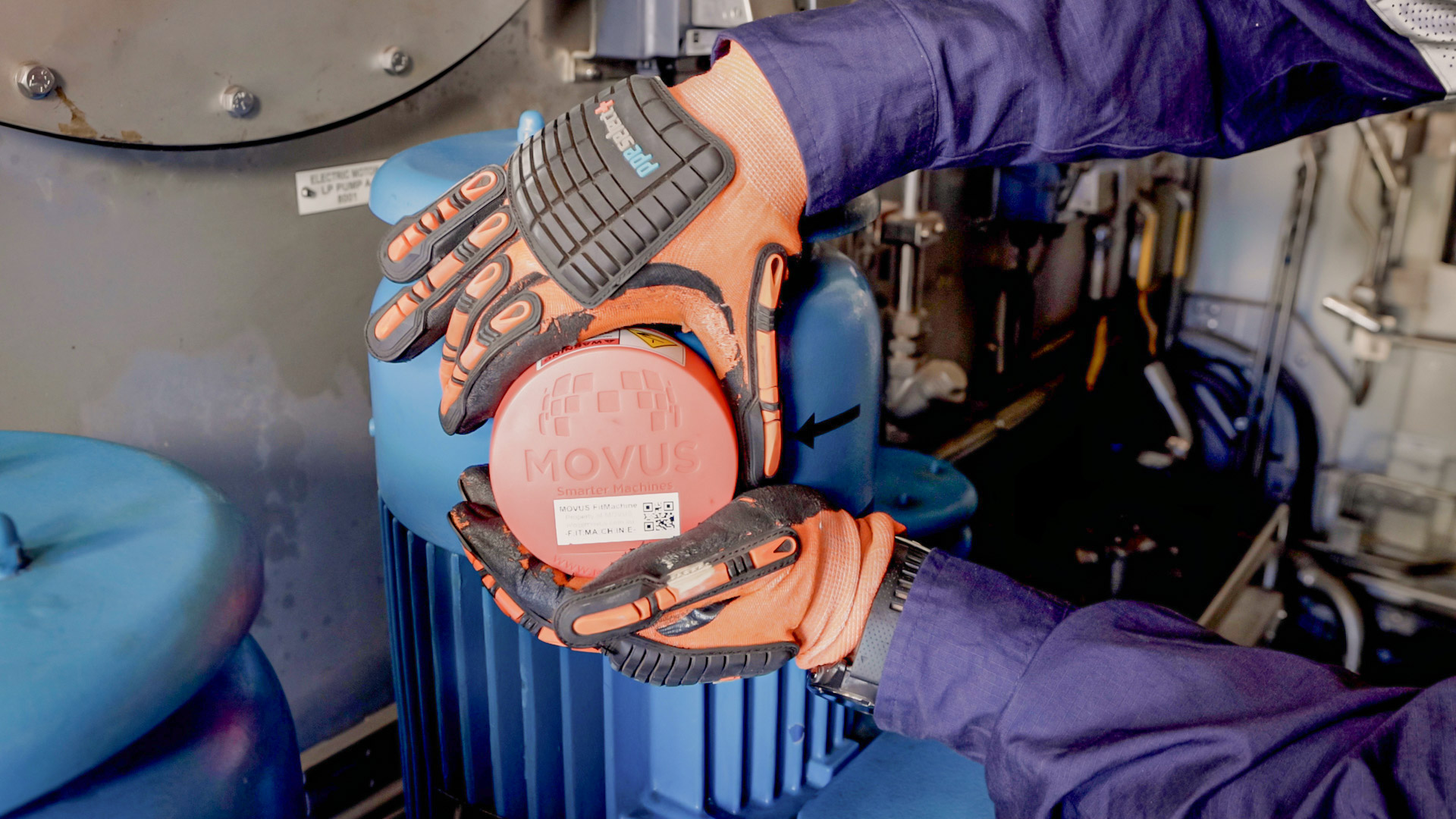
The FitMachine Sensor is easy to install, and after some simple activation steps, sends data to the FitMachine Dash platform. After an initial learning period, a ‘normal state’ is established for monitored equipment, and conditional alerts are automatically generated for system users.
FitMachine sensors are ideally suited for monitoring fans, compressors, motors, pumps and more. There is also an intrinsically safe option suitable for explosive oil and gas environments.
HCS sees huge potential for the provision of additional monitoring services to help customers achieve increased equipment uptime and reliability.
The FitMachine solution provides a turnkey method of delivering predictive and condition-based maintenance as a service.
MOVUS Australia is the manufacturer of the FitMachine, a non-intrusive IIoT sensor that monitors the temperature, acoustics and vibration of operating industrial equipment, as well as a cloud-based platform providing access to the generated data streams.
A RealWear support call showing a FitMachine installation
The cost of a MOVUS FitMachine could be considered a negligible part of an industrial asset’s maintenance program. Its installation is remarkably simple.
However, due to their access to RealWear assisted-reality headsets and the availability of MOVUS’ dedicated customer success team, HCS decided to hold an assisted reality onsite video call to validate the device placement plan.
Assisted-reality headsets display content on a digital screen mounted on a small boom arm, positioned in the wearer's field-of-view, providing information as needed without overly distracting the user, thus enabling them to maintain situational awareness while performing work tasks.
The video at the top of this article contains the recorded MOVUS support call. The call is made with a RealWear Navigator 500 device powered by Onsight Connect software.
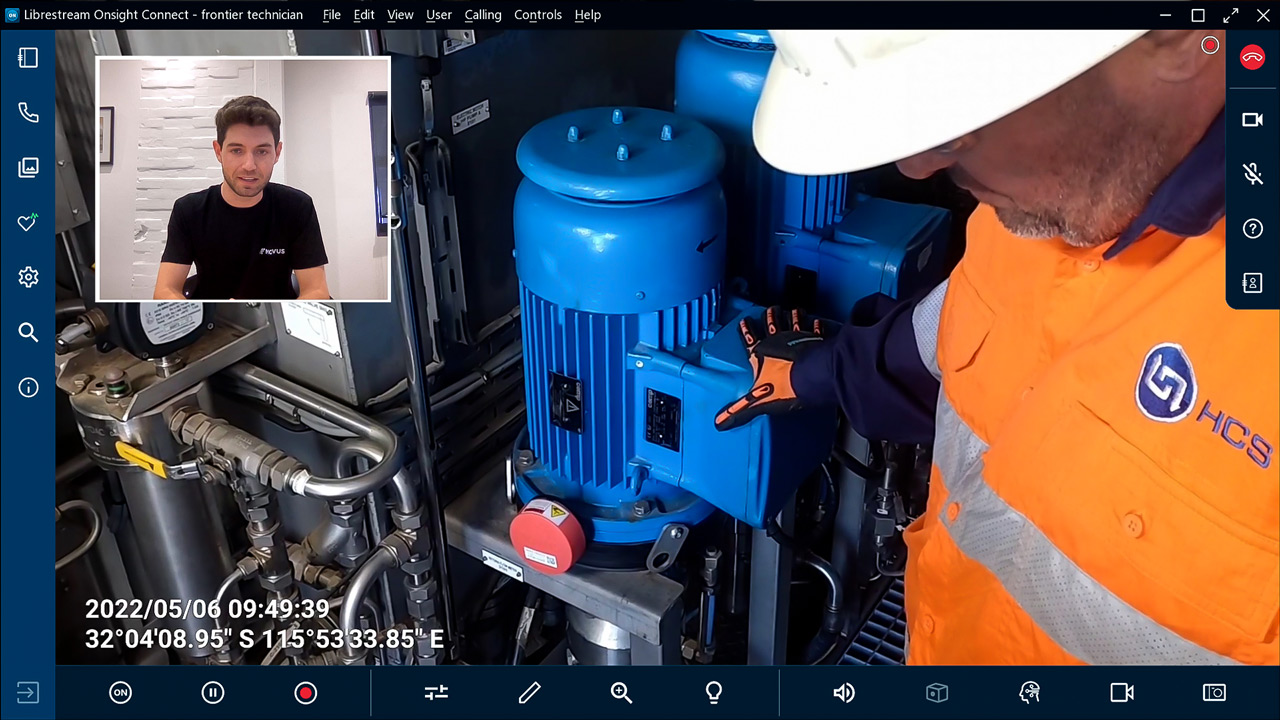
As demonstrated in the video, accessing remote expert assistance in an industrial environment is made simple with the use of AR headsets and appropriate software.
Hands-free operation and rich annotation features provide support technicians with powerful communication tools without the need to travel to site and validate correct installation and configuration of equipment.
HCS plan future use of RealWear and MOVUS technologies
HCS is planning to expand its use of RealWear headsets and Librestream software. Jon Clancy’s team is currently investigating additional use-cases for hands-free, paperless maintenance inspections, and the use of digital work instructions.
MOVUS FitMachines are also being further evaluated to find monitoring conditions that will alert specific maintenance issues and deliver tangible cost benefits to HCS customers.
Tips on implementing remote expert assistance
Here are some recommended general steps to successfully implement an AR remote expert assistance solution within your own operations:
- Develop a business case estimating the costs and time saved by enabling frontline technicians to communicate with remote experts.
- Investigate existing network connectivity at the locations where work occurs and build any required infrastructure.
- Engage with qualified AR resellers to advise on the specifications of required device hardware, accessories, and software.
- Run in-field trials and use learnings to develop internal training content and assign solution champions to support program.