Faced with pressure to move the manufacture of his cranes overseas to scale and remain competitive, Kevrek Managing Director Terry O'Neill opted to install a robotic arm at his Perth workshop. Initially unsure of the outcome, his decision successfully kept his world-class product local and helped scale his business fivefold.
Faced with a dilemma: raise prices or manufacture offshore
Terry saw huge potential for his locally manufactured, vehicle-mounted cranes in other Australian states and across the wider Asia-Pacific region. However, originally all Kevrek cranes were fabricated and assembled manually at their local workshop in Malaga. Already at maximum capacity servicing existing local customers, he knew he needed to find a way to drastically increase his production capability.

Terry quickly met with a dilemma: he needed to maintain cost competitiveness against inferior products made overseas. However, a feasibility investigation revealed he would need to relocate core manufacture offshore or import and re-badge an inferior product. Simply adding more local fabrication workers would not make the numbers work out.
Potential manufacturing partners were found in both China and Malaysia, but Terry felt very uneasy about displacing his current workforce and losing control of his high-quality product.
Customers prefer Kevrek cranes due to their operational versatility, hydraulic arms, variety of install options, and light weight that doesn’t take away too much load-carrying capacity of a vehicle. Their cranes are popular with utility companies, state and local government, commercial businesses, as well as marine, mining and agricultural operations.
Kevrek manufactures a series of market leading, rugged vehicle mounted cranes with load capacities from 550kg up to 1250kg. The cranes are used by customers to safely load and unload heavy weight objects from utes, light trucks and trailers.
Robotic automation to supercharge the existing workforce
As he researched further, Terry considered whether robotic automation could solve his problem. Although not in common use at the time, he had heard of industrial robotic arms and wondered whether they could be used to help supercharge his existing fabrication team.
The most significant bottleneck in the Kevrek fabrication process was arc welding the crane base frames and extensions. Terry hoped he could retrain his existing workers to operate a welding robot, significantly reduce welding time, and dramatically increase the number of cranes being produced each month.
Robotic arms are robust mechanical arms with multiple joints that are precisely programmed to move along tracks and rotate on an axis in all directions. The arms can be fitted with a variety of tools to work with industrial materials and complete production tasks such as picking up, placing down, twisting, turning, heating, bending, and welding.
Acquiring one of the first FANUC arc welding robots in Australia
As an early adopter, Terry wanted to see a robot in action, but wasn’t able to locate any operating robots in Perth. After further investigation, he found a manufacturer in Melbourne who had recently integrated a robotic arm. He made some inquiry phone calls, and after a gracious invitation, quickly found himself on a plane to see the technology for himself.
Terry was very impressed with what he saw in Melbourne. He decided to move forward and obtained the third FANUC arc welding robot bought in Australia. The arm could be programmed to accommodate the variety of different crane models and could use a rotating base jig to minimise positioning work from an operator.

The implementation of the robot proved to be intensive. The installation, configuration and testing of the machine ended up incurring eight times the cost of the hardware.
However, the knowledge Terry gathered from the trip to Melbourne had certainly made the implementation easier, and the required effort more predictable. Terry maintained confidence that the technology was right, and the solution was sound.
FANUC is a world leading supplier of industrial robots and factory automation products, including CNC systems, IoT solutions, drilling products, cobots, and laser cutting systems. Founded in 1956, it has the largest range of robots, including market-leading ARC Mate Series welding robots suitable for MIG and TIG welding or plasma and laser cutting.
A solution exceeding expectations and intriguing customers
It turned out that the robot was able to take over 90% of the required welding. There was a significant reduction in welding times, which was much faster than expected. "One weld which was taking the guys 38 minutes, the robot now does that in three and a half minutes," shared Terry. "So, that pretty well explains itself."
He went on to say, "The thing with that machine is every weld is the same. It's not different from one person to another person, from an eight o'clock job, to a five o'clock job. Everything is exactly the same right throughout the whole operation. Our warranty is less than 0.2%."
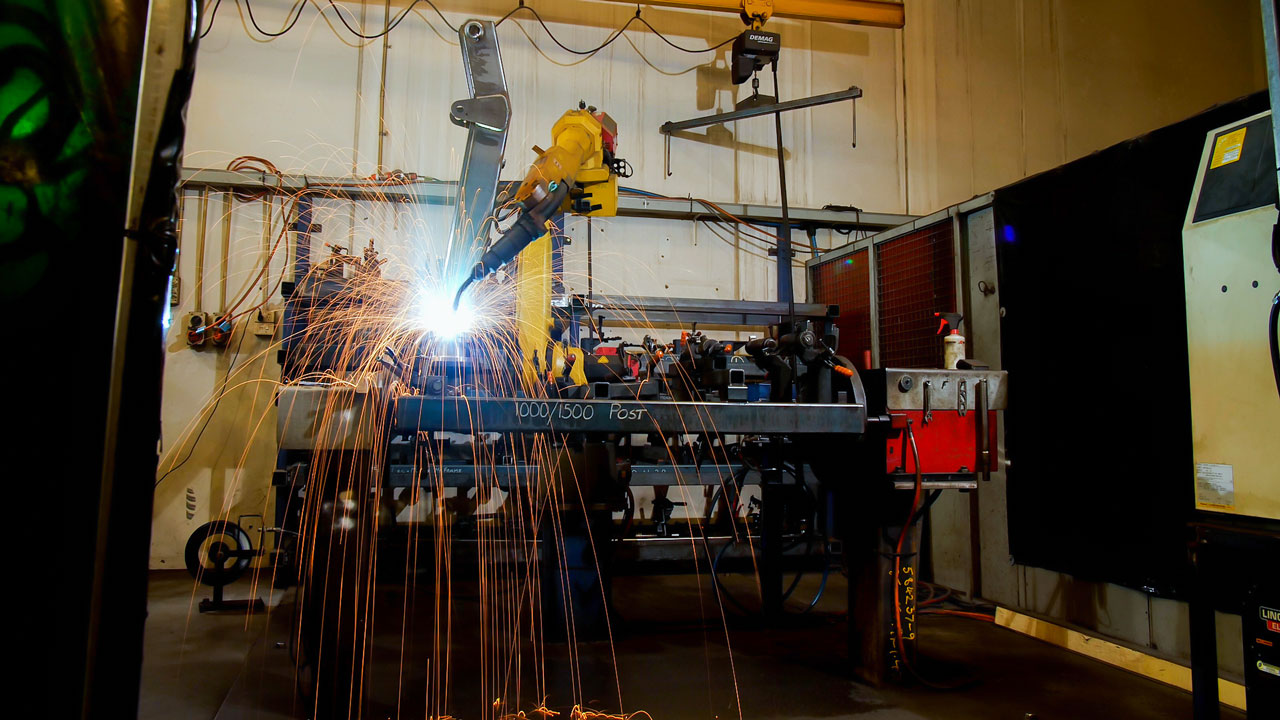
After installing the robot, Kevrek grew production from 10-12 cranes per month to 60-70, fulfilling their original goal of keeping their manufacturing in Malaga. The business was able to pay off the investment within two years, which was well ahead of the five years originally planned.
There were added safety benefits for the workers, minimising dangerous and monotonous work, while allowing them to focus on high-value tasks. The original lead-welder was retrained and still operates the robotic arm today. Terry laughed, "It's Liam's toy and nobody else's!" He has, of course, trained other operators for contingency.
Many customers are intrigued by the process, "People are coming in when they hear about it, they want to come, and people make special trips, even the country clients, to look at the machine in operation. And they're just super impressed."
Looking forward to a larger robotic workforce
Whilst originally wary of the large commitment, Terry ended up very pleased he decided to progress with the robotic welding arm implementation.
"I feel really good with the product and I say quite frankly that our product is, in its size and make, the best in the world, or as good as the best in the world," Terry said proudly.
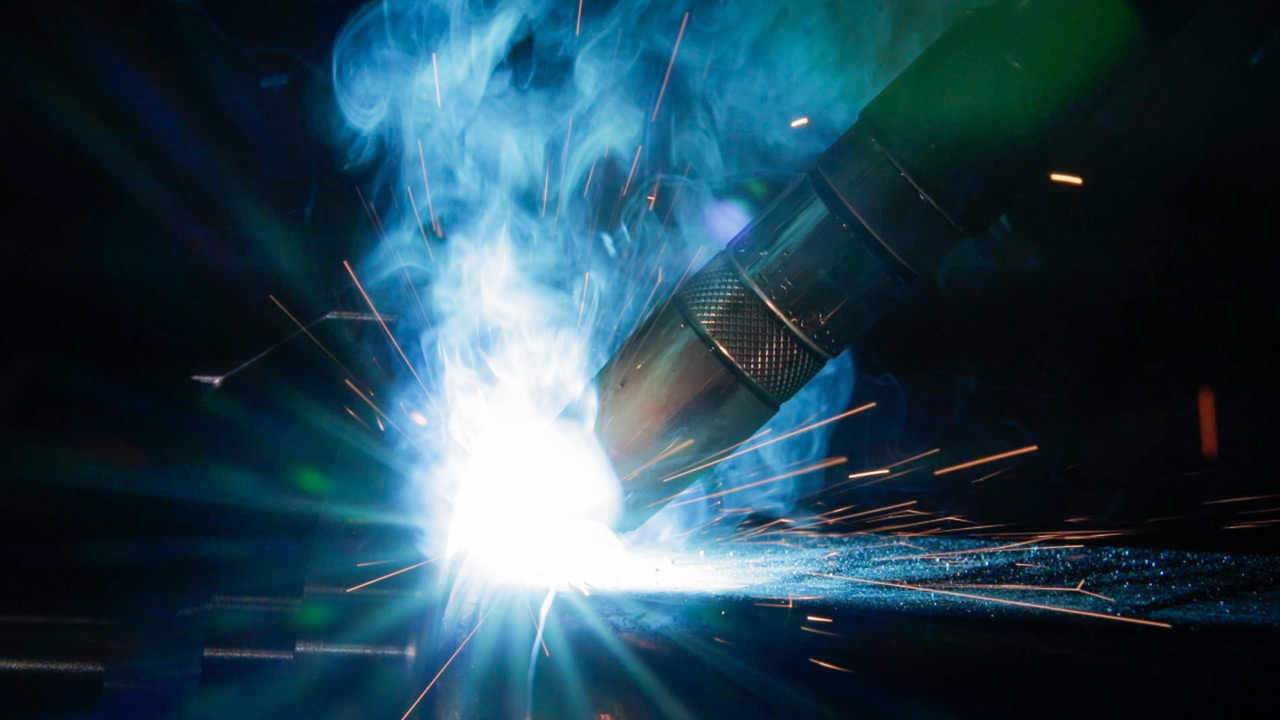
Increasing production didn't end up saturating the market; the Kevrek products just got even better and so did the demand. The outlook is positive, with agriculture, mining and utility companies all currently buying more cranes.
Terry hopes to continue to grow the business and looks forward to the day when his existing welding arm has additional robotic colleagues working alongside.
Investing in robotics will pay off if done right
Kevrek’s experience demonstrates the ability of automation technology to significantly scale a manufacturing operation, within an existing workshop, supported by an existing workforce. Although making a large initial investment, they later upgraded the original robot at a quarter of the cost, with the price of the technology consistently dropping over time.
Terry O’Neill strongly recommends the use of automation to businesses that hope to retain local manufacturing, “People just seem to think these days it's cheaper to manufacture overseas. If they can set it up, robotics will certainly pay for itself.”
Kevrek gained valuable insights from their experience implementing robotic automation:
- During investigation, seek advice from other businesses that use similar robots, even if they are not from within your industry.
- In addition to the hardware costs, ensure that you have allocated enough budget for the installation, testing and configuration.
- Beware that robots will manufacture with consistent quality, but if not configured correctly, they will consistently produce errors.
- In their case, robotics was able to take over more of the manual work than expected, and with greater productivity than hoped.